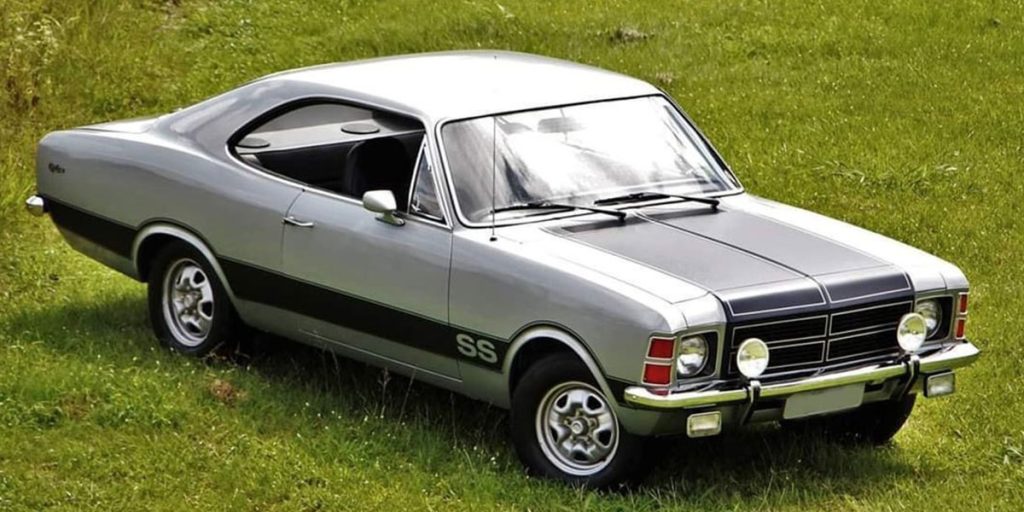
Muscle Cars of the ’60s and ’70s Shaped the Global Automotive Industry
American muscle car’s didn’t just change the automotive landscape in America, it changed the global automotive industry forever. Born from a perfect storm of post-war
These days there is a dwindling supply of classic muscle cars left in the wild for an enthusiast or collector to restore, especially good condition shells. Anyone hoping to bring one of these classics back from the grave is inevitably going to have to address portions of the body that have rusted away.
Known as sheet metal, these body panels and other structural components are available from several different brands and can be ordered as full replacement panels or just patches, which can seem daunting to those inexperienced in restoration.
Today we’re here to break down some of the differences and nuances when it comes to all things sheet metal so that you can make an informed choice for your restoration project.
All sheet metal should be test fitted, prepped, and then worked to ensure the best possible fitment. This applies to the best panels on the market today and even new-old-stock of the originals.
You should expect all panels to exhibit minor imperfections such as scratches, dimples, etc. This is a normal occurrence as the parts are expected to be prepped, scuffed, and filled before paint and final installation onto the vehicle.
Tolerances and panel gaps will vary with each vehicle. Generally, cars manufactured during this automotive era were hand-assembled by workers at the factory, well before today’s modern robotic manufacturing processes that produce consistent results.
No two vehicles have identical gaps even on two vehicles produced back to back, due to the nature of hand assembly. Various tricks were used to align the panel gaps, such as adding shims and elongating mounting holes to get panels closer to one another and reduce gapping. Rarely did panels fit perfectly in place without adjustment during the factory assembly process. This can be especially true if the vehicle has ever raced, been in an accident, or had extensive modifications to the body or frame during its history. Even something as simple as sitting in a field or barn for years can affect the straightness of a vehicle’s frame. Any number of situations can influence how a panel may fit on a particular vehicle, unlike modern cars.
Most reproduction sheet metal is thinner than original sheet metal. The typical thickness of products on the market today is generally between 18 to 22 gauge metal, with the most common being 20 gauge. Original sheet metal was typically around 16 gauge in thickness.
This can have a number of side effects. A thinner gauge of metal means that it is lighter and less dense, which ultimately results in reduced weight of the vehicle compared to an all original example. Thinner panels also mean that they can be easier to prep and work into the correct alignment and fitment on the body of the vehicle compared to an NOS piece.
While a full, bolt-on replacement panel may seem like the easier route to take in most cases, depending on the severity of the damage, location, and type of panel, a patch may be the preferred choice. Smaller patches allow the preservation of the original sheet metal if there is minimal corrosion or damage. Patches are also much less expensive than replacing an entire panel in one shot, and of course are generally cheaper to ship than a full sized panel that would require a freight shipment.
However, certain areas that have multiple smaller instances of corrosion/damage may be better off simply replacing the entire panel rather than making a swiss cheese patchwork. This will also preserve the strength of certain areas better than cutting and patching portions, as this reduces the integrity of the panel. Fully replacing an entire panel can also be a simpler installation than welding in a patch.
Either method has pros and cons, it ultimately depends on the type and location of the panel as well as the extent of the affected area. Retaining a body line is much easier by using a full panel, as is replacing a full or half floor. Alternatively, If the lower wheel arch is the only affected area on the quarter panel then a patch may be the better option in these cases.
Replacement sheet metal will be coated with one of these two materials, instead of being sold as bare metal. Both of these coatings are a major improvement to the original sheet metal, as standard practice in the past only used spray guns, which would have trouble reaching certain tight fit areas with the factory paint.
EDP is the most common coating, which stands for Electrophoretically Deposited Primer. This coating not only helps to prevent rusting of the new panel, but also provides protection against contaminants during transit or while in storage.
The sheet metal is electrically charged and then placed into a bath, which attracts an even layer of primer across the entire surface of the panel. EDP can be left on the panel safely as an additional layer of protection under the standard primer and paint but should be sanded/removed at any points where the panel will be welded.
See more about EDP in this Article: What in the EDP is on my brand new body Repair Panel?
Weld-Thru Primer is a similar protective coating, however as the name implies it promotes protection of the metal after/during welding. This is useful with welding-in panels as the special primer adds a layer of protection under the weld points, preventing future corrosion and rust from forming at the welds as well as filling in impurities in the metal itself. Weld-thru primer requires less preparation than EDP coated sheet metal.
Most panels are manufactured overseas, typically in Taiwan and China. Some limited brands may have certain parts manufactured in the US, but not many generally are as the higher labor costs become prohibitive and are passed on to the consumer.
The majority of the reproduction sheet metal on today’s market utilizes tooling that is often created from molds of NOS products. While some brands may have commissioned their own dies for certain parts, often times the stamps are shared among the various brands. Depending on the age of the tooling and how worn it becomes over time, the creases and body lines may be more or less defined. Not much of the original GM tooling is still in operation, and the quality of N.O.S. parts steadily decreased the longer the particular die had been in operation as it wore out over time.
Multiple different manufacturer part numbers will be listed on the same label. The reason for this practice is the shared source of origin at the stamping facility. The fit and finish between these brands is interchangeable but Company A may have different tolerances than Company B does. That is why there will often be a Goodmark, Golden Legion, or Dynacorn part number all on the same panel. The determining factor isn’t so much the brand as it is the current quality of the tooling and the operator of the machinery.
While smaller patch panels can ship normally via UPS, larger panels such as doors, hoods, quarter panels and so on will require shipping via truck freight by a freight carrier. These items are too large to ship via Standard Ground or expedited methods and require being strapped to a pallet in order to ship out.
The best practice is to have a commercial address in mind as the shipping address in this situation, as the location needs to accommodate the tractor trailer. This applies to the tractor trailer’s ability to access the location as well as unloading the shipment from the vehicle. The delivery carrier has final say in determining whether an address qualifies as commercial.
American muscle car’s didn’t just change the automotive landscape in America, it changed the global automotive industry forever. Born from a perfect storm of post-war
Is your ’67 Chevelle SS The Real Deal? Enthusiasts love classic cars for all sorts of reasons such as the looks, performance, history, and nostalgia.
When it comes to restoring or verifying the originality of your Chevelle, correctly identifying the small block under the hood an important step. After all,